Fasteners and Machining: Essential Elements for Accuracy Production
Fasteners and Machining: Essential Elements for Accuracy Production
Blog Article
Navigating the Globe of Fasteners and Machining: Techniques for Accuracy and Speed
In the detailed realm of bolts and machining, the quest for precision and rate is a continuous challenge that requires meticulous interest to information and strategic preparation. From understanding the varied range of bolt types to choosing optimal materials that can stand up to rigorous needs, each action in the process plays a crucial function in achieving the wanted outcome. Precision machining methods better elevate the complexity of this craft, calling for a fragile balance between technical competence and cutting-edge approaches. As we look into the approaches that can boost both rate and efficiency in this domain, the interplay between quality control steps and operational excellence emerges as a crucial prime focus.
Understanding Fastener Types
When choosing fasteners for a project, understanding the various kinds readily available is essential for ensuring optimal efficiency and integrity. Fasteners come in a wide variety of types, each made for certain applications and demands. Bolts are used with nuts to hold products with each other, while screws are flexible fasteners that can be used with or without a nut, relying on the application. Nuts, on the various other hand, are internally threaded fasteners that friend with screws or bolts, providing a safe and secure hold. Washing machines are necessary for dispersing the tons of the fastener and preventing damages to the material being fastened. In addition, rivets are long-term fasteners that are perfect for applications where disassembly is not required. Recognizing the distinctions between these bolt kinds is essential for picking the right one for the task, making sure that the link is solid, long lasting, and reputable. By choosing the proper fastener kind, you can optimize the efficiency and durability of your project - Fasteners and Machining.
Selecting the Right Materials
Understanding the relevance of picking the appropriate products is vital in making sure the optimum efficiency and dependability of the selected fastener kinds talked about formerly. When it comes to fasteners and machining applications, the product selection plays a crucial duty in determining the overall strength, toughness, deterioration resistance, and compatibility with the desired setting. Various products supply differing residential properties that can significantly impact the performance of the bolts.
Common materials used for fasteners consist of steel, stainless-steel, light weight aluminum, titanium, and brass, each having its unique strengths and weaknesses. Steel is renowned for its high strength and sturdiness, making it appropriate for a large range of applications. Stainless steel provides outstanding rust resistance, suitable for atmospheres prone to moisture and chemicals. Light weight aluminum is corrosion-resistant and light-weight, making it ideal for applications where weight decrease is crucial. Brass is typically selected for its aesthetic appeal and exceptional conductivity. Titanium is understood for its exceptional strength-to-weight ratio, making it perfect for high-performance applications. Choosing the ideal material involves considering variables such as toughness demands, environmental problems, and spending plan restrictions to make sure the desired efficiency and long life of the fasteners.
Precision Machining Techniques
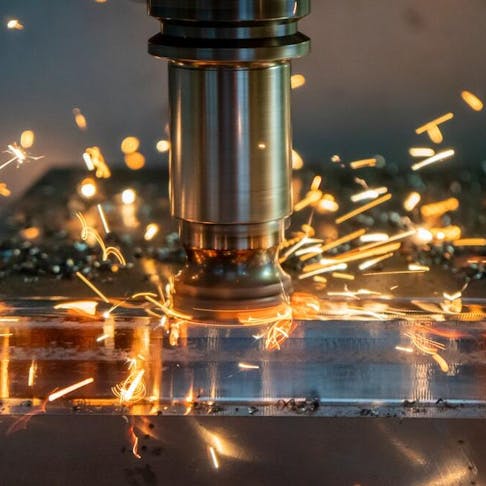
In addition to CNC machining, various other precision strategies like grinding, turning, milling, and boring play vital functions in fastener manufacturing. Grinding assists achieve great surface area coatings and limited dimensional tolerances, while turning is typically used to produce round elements with accurate diameters. Milling and exploration operations are important for shaping and creating openings in fasteners, guaranteeing they meet specific requirements and feature correctly.
Enhancing Speed and Performance
To maximize fastener production processes, it is necessary to simplify operations and execute reliable strategies that complement precision article machining methods. One vital strategy for enhancing speed and effectiveness is the application of lean production concepts. By reducing waste and concentrating on continuous enhancement, lean methods web link aid remove traffic jams and optimize process. Furthermore, spending in automation technologies can significantly increase production speed. Automated systems can deal with repeated jobs with precision and speed, allowing workers to concentrate on even more facility and value-added activities. Taking On Just-In-Time (JIT) inventory administration can additionally enhance efficiency by ensuring that the best products are readily available at the correct time, reducing excess stock and reducing lead times. Cultivating a society of partnership and interaction among group members can boost overall performance by advertising transparency, problem-solving, and innovation. By combining these strategies, makers can attain an equilibrium in between speed and accuracy, ultimately enhancing their one-upmanship in the bolt market.
Top Quality Control Measures
Carrying out strenuous top quality control measures is essential in making certain the reliability and uniformity of fastener items in the production procedure. Fasteners and Machining. Quality control steps encompass various stages, beginning from the choice of raw products to the final evaluation of the finished bolts. This involves examining variables such as material stamina, structure, and sturdiness to guarantee that the fasteners meet industry requirements.
Normal calibration of equipment and machinery is important to maintain uniformity in production and make sure that bolts satisfy the needed resistances. Applying strict methods for recognizing and resolving non-conformities or defects is vital in stopping substandard products from entering the marketplace. By developing an extensive high quality control framework, producers can maintain the credibility of their brand name and supply fasteners that satisfy the greatest standards of performance and durability.
Final Thought
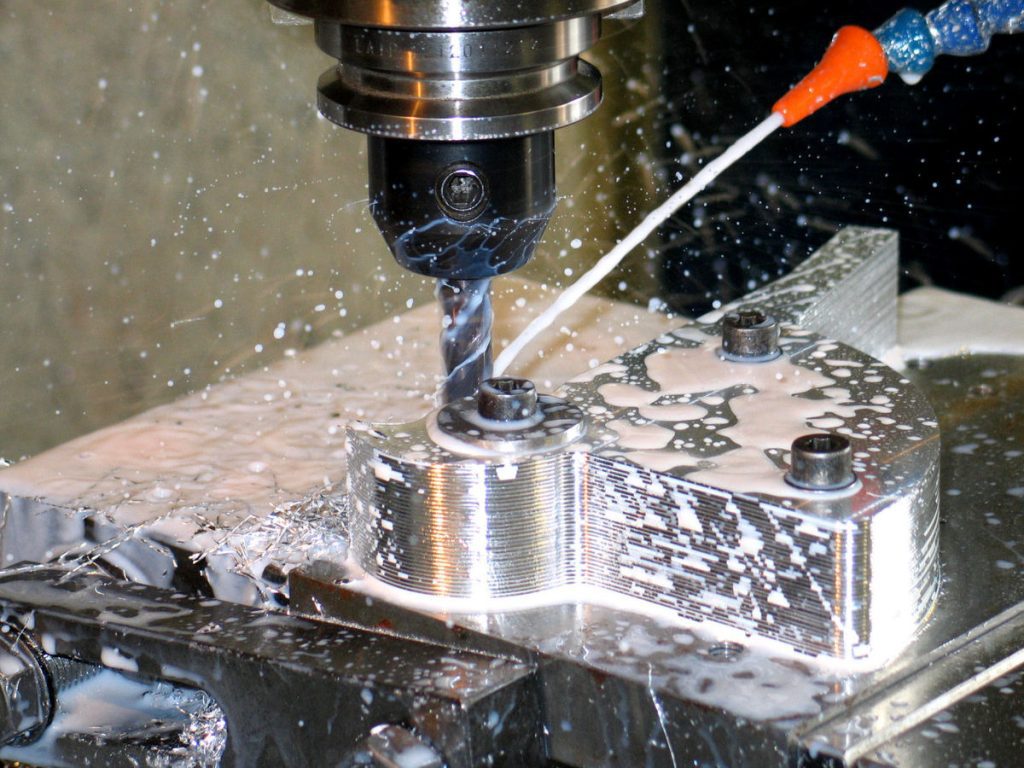
In the complex realm of bolts and machining, the quest for precision and speed is a continuous obstacle that requires careful interest to information and critical preparation. When it comes to bolts and machining applications, the material choice plays an essential function in figuring out the general toughness, sturdiness, rust resistance, and compatibility with the desired setting. Accuracy machining involves various sophisticated techniques that guarantee the tight tolerances and specs required for bolts.In enhancement to CNC machining, other accuracy methods like grinding, turning, milling, and exploration play essential functions in fastener manufacturing.To maximize bolt manufacturing procedures, it is crucial to simplify operations and implement effective techniques that enhance precision machining methods.
Report this page